전자동 웨이퍼 링 절단 장비 작업 크기 8인치/12인치 웨이퍼 링 절단
기술적 매개변수
매개변수 | 단위 | 사양 |
최대 작업물 크기 | mm | ø12인치 |
축 | 구성 | 단일 스핀들 |
속도 | 3,000~60,000rpm | |
출력 전력 | 30,000분에서 1.8kW(2.4 옵션)⁻¹ | |
최대 블레이드 직경 | Ø58mm | |
X축 | 절단 범위 | 310mm |
Y축 | 절단 범위 | 310mm |
단계 증가 | 0.0001mm | |
위치 정확도 | ≤0.003mm/310mm, ≤0.002mm/5mm (단일 오차) | |
Z축 | 움직임 해결 | 0.00005mm |
반복성 | 0.001mm | |
θ축 | 최대 회전 | 380도 |
스핀들 유형 | 링 절단을 위한 견고한 블레이드가 장착된 단일 스핀들 | |
링 절단 정확도 | μm | ±50 |
웨이퍼 위치 정확도 | μm | ±50 |
단일 웨이퍼 효율 | 분/웨이퍼 | 8 |
다중 웨이퍼 효율성 | 최대 4개의 웨이퍼를 동시에 처리 | |
장비 무게 | kg | 약 3,200 |
장비 치수(폭×깊이×높이) | mm | 2,730 × 1,550 × 2,070 |
작동 원리
이 시스템은 다음과 같은 핵심 기술을 통해 뛰어난 트리밍 성능을 달성합니다.
1. 지능형 모션 제어 시스템:
· 고정밀 리니어 모터 구동 (반복 위치 정확도: ±0.5μm)
· 복잡한 궤적 계획을 지원하는 6축 동기 제어
· 실시간 진동 억제 알고리즘으로 절단 안정성 보장
2. 고급 감지 시스템:
· 통합 3D 레이저 높이 센서(정확도: 0.1μm)
· 고해상도 CCD 시각 위치 지정(5메가픽셀)
· 온라인 품질 검사 모듈
3. 완전 자동화된 프로세스:
· 자동 로딩/언로딩(FOUP 표준 인터페이스 호환)
· 지능형 분류 시스템
· 폐쇄형 세척 유닛(청정도 10등급)
일반적인 응용 프로그램
이 장비는 반도체 제조 애플리케이션 전반에 걸쳐 상당한 가치를 제공합니다.
응용 분야 | 공정 재료 | 기술적 이점 |
IC 제조 | 8/12인치 실리콘 웨이퍼 | 리소그래피 정렬을 향상시킵니다. |
전력 장치 | SiC/GaN 웨이퍼 | 모서리 결함을 방지합니다 |
MEMS 센서 | SOI 웨이퍼 | 장치 안정성을 보장합니다 |
RF 장치 | GaAs 웨이퍼 | 고주파 성능 향상 |
고급 패키징 | 재구성된 웨이퍼 | 포장 수율 증가 |
특징
1. 높은 처리 효율을 위한 4개 스테이션 구성
2. 안정적인 TAIKO 링 탈착 및 제거
3. 주요 소모품과의 높은 호환성
4.다축 동기 트리밍 기술은 정밀한 모서리 절단을 보장합니다.
5. 완전 자동화된 공정 흐름으로 인건비가 크게 절감됩니다.
6. 맞춤형 작업대 설계로 특수 구조의 안정적인 처리가 가능합니다.
기능
1. 링 드롭 감지 시스템
2. 자동 작업대 청소
3. 지능형 UV 탈착 시스템
4.작업 로그 기록;
5.공장 자동화 모듈 통합;
서비스 약속
XKH는 생산 과정 전반에 걸쳐 장비 성능과 운영 효율성을 극대화하도록 설계된 포괄적이고 완전한 수명 주기 지원 서비스를 제공합니다.
1. 맞춤형 서비스
· 맞춤형 장비 구성: 당사 엔지니어링 팀은 고객과 긴밀히 협력하여 특정 소재 특성(Si/SiC/GaAs) 및 공정 요구 사항에 따라 시스템 매개변수(절단 속도, 블레이드 선택 등)를 최적화합니다.
· 프로세스 개발 지원: 에지 거칠기 측정 및 결함 매핑을 포함한 자세한 분석 보고서와 함께 샘플 처리를 제공합니다.
· 소모품 공동 개발: 새로운 소재(예: Ga₂O₃)의 경우, 당사는 선도적인 소모품 제조업체와 협력하여 응용 분야별 블레이드/레이저 광학 장치를 개발합니다.
2. 전문적인 기술 지원
· 전담 현장 지원: 인증된 엔지니어를 중요한 램프업 단계(일반적으로 2~4주)에 배정하여 다음을 담당합니다.
장비 교정 및 프로세스 미세 조정
운영자 역량 교육
ISO 5등급 클린룸 통합 지침
· 예측 유지 관리: 진동 분석 및 서보 모터 진단을 통한 분기별 상태 점검을 통해 계획되지 않은 가동 중지를 방지합니다.
· 원격 모니터링: IoT 플랫폼(JCFront Connect®)을 통해 장비 성능을 실시간으로 추적하고, 자동 이상 경보를 발송합니다.
3. 부가가치 서비스
· 프로세스 지식 기반: 다양한 소재에 대한 300개 이상의 검증된 절단 레시피에 액세스하세요(분기별로 업데이트).
· 기술 로드맵 정렬: 하드웨어/소프트웨어 업그레이드 경로(예: AI 기반 결함 감지 모듈)를 통해 투자를 미래에 대비시킵니다.
· 긴급 대응: 4시간 원격 진단 및 48시간 현장 개입 보장(글로벌 커버리지).
4. 서비스 인프라
· 성능 보장: SLA 지원 응답 시간을 통해 98% 이상의 장비 가동 시간을 계약에 따라 보장합니다.
지속적인 개선
저희는 서비스 제공을 강화하기 위해 반기별 고객 만족도 조사를 실시하고 카이젠(Kaizen) 이니셔티브를 시행합니다. 저희 R&D 팀은 현장에서 얻은 통찰력을 장비 업그레이드에 적용합니다. 펌웨어 개선의 30%는 고객 피드백을 통해 이루어집니다.
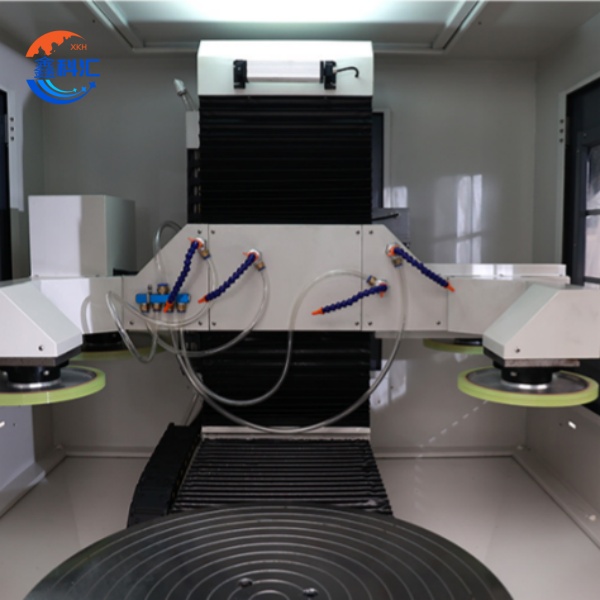
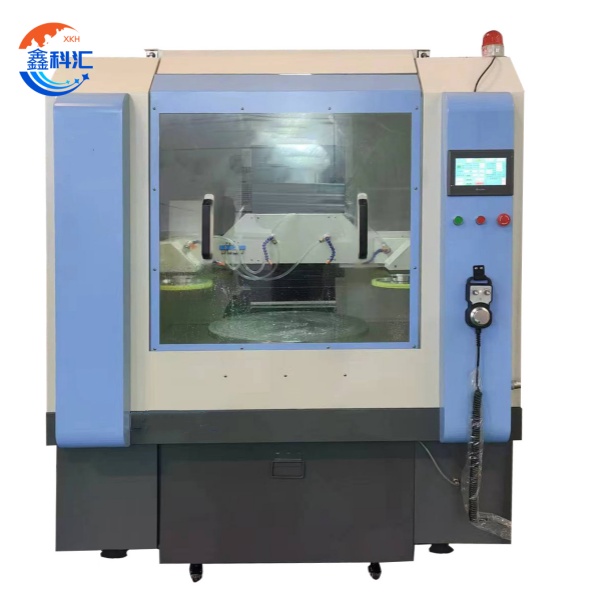